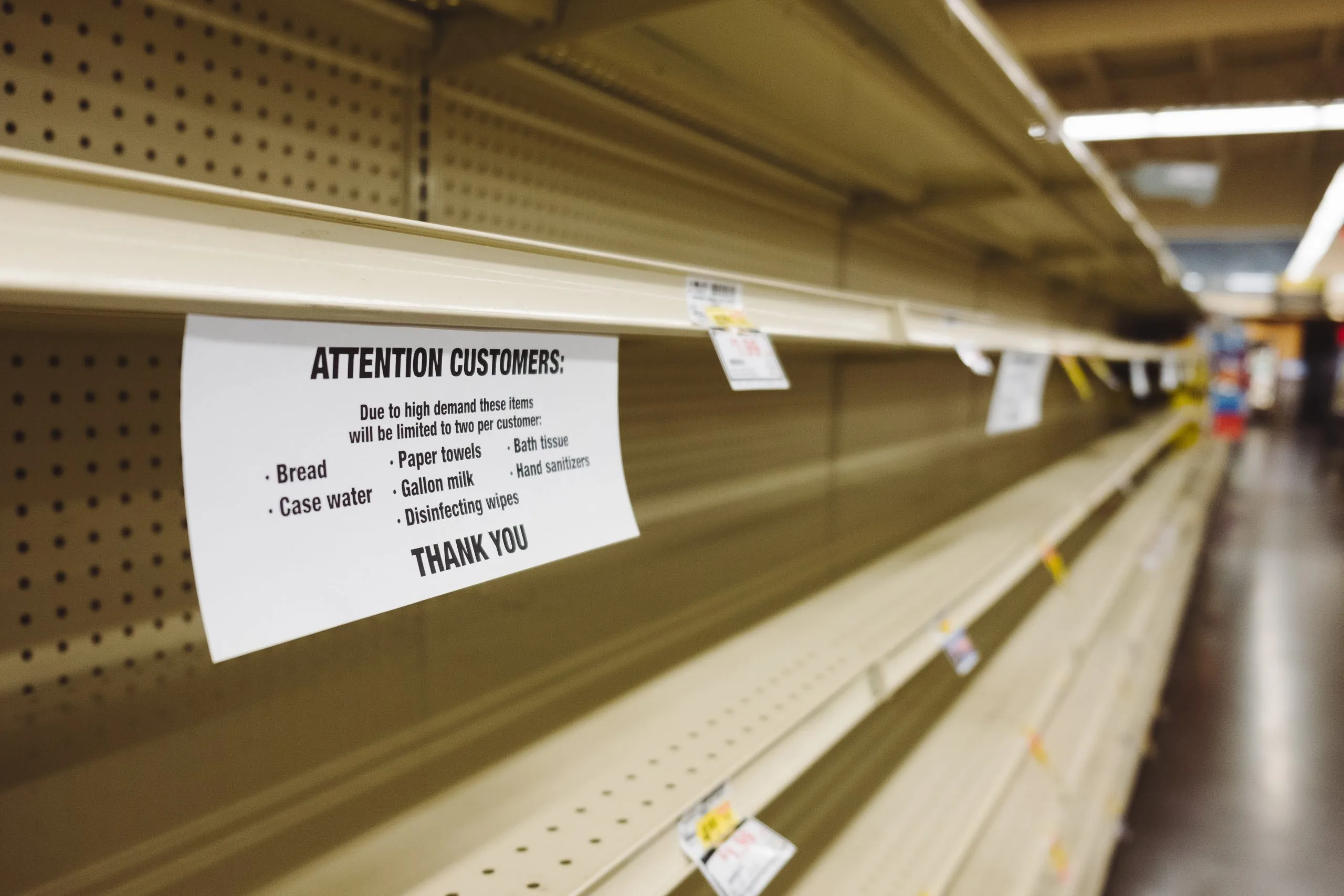
In some cases, unexpected increases in demand and/or delivery problems lead your stock level to drop faster than expected. In these cases, it’s important to maintain safety stock to deal with these situations. What is safety stock, why do you need this buffer, and what could go wrong if you don’t have it? How do you determine and calculate the right safety stock level for your company? In this blog, we explain how to control your stock levels and purchasing via safety stock.
What is safety stock?
Your warehouse is the center of all order flows. Purchasing decisions and company processes keep your stock moving. However, in some situations, your stock level may decrease faster than expected. Orders may be delayed due to problems in the production phase and/or delivery process, and demand may rise faster than supply is replenished. A supply and demand imbalance can occur.
Safety stock is the buffer that controls unexpected stock changes. It lowers the risk that stock shortages interrupt customer demand and cause lost sales. There are three frequent situations when you need safety stock.
1. Uncertain customer and market demand
Market demand can change unexpectedly and cause faster shrinkage of your stock than the supplies are replenished. Your safety stock absorbs this.
2. Uncertain delivery times
Production and transport problems can delay the deliveries of your purchases. The safety stock allows you to still meet customer demand, while the delayed orders are in transit.
3. Uncertain deliveries of suppliers
Your suppliers may struggle to deliver orders due to production problems and/or internal logistical delays. The safety stock prevents your clients from suffering because of supplier issues.
The safety stock is a buffer that helps you to meet customer demand under unexpected circumstances. In the following sentences, you will read why you need safety stock.
Why do you need safety stock?
Safety stock makes your company more resilient. This buffer allows you to retain control, regardless of market demand and the wider supply chain. It makes sure that you can continue to deliver when demand surges or supply problems threaten your stock level.
The main reason to keep safety stock is to be able to continue serving your customers. Whether there’s an interruption in the supply chain or an error in your purchasing planning, this buffer gives you time to solve this problem.
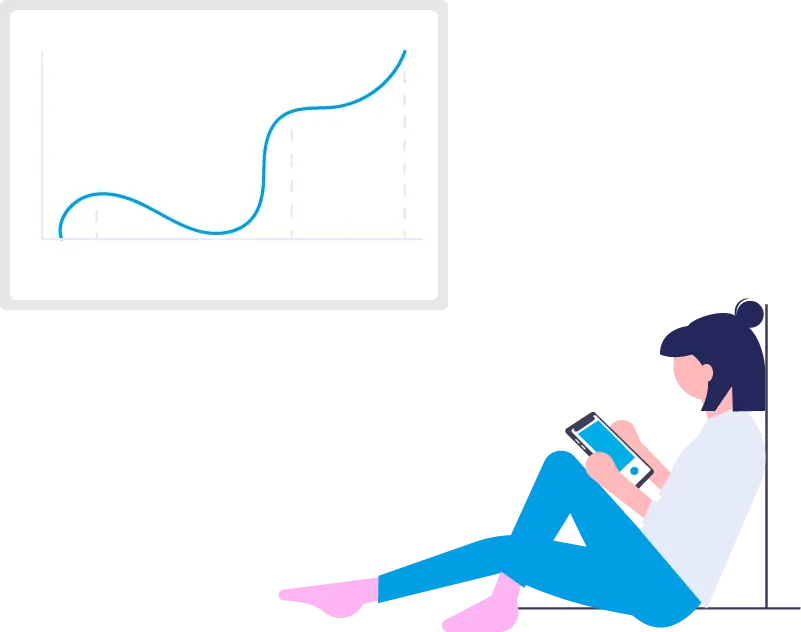
More resilient to seasonalities
Safety stock makes you more resilient against seasonalities and trends. If you combine data-driven forecasting and the use of safety stock, you can also meet customer demand under exceptional circumstances.
Absorb supply problems from your suppliers
The safety stock helps you absorb supply problems from your suppliers. A provider can promise short delivery times, but that may not match reality.
If you have to use your safety stock more often with a specific supplier, it might be a sign that you may need to reassess using this supplier or renegotiate terms.
If you do not keep any safety stock or if you try to work with a minimal stock, you may not be able to meet customer demand due to increased demand and/or longer delivery times.
How often are you willing to say no? What are the consequences of not keeping safety stock?
What are the consequences if you don’t keep safety stock?
If safety stock is not part of your purchasing planning, you may have to disappoint your customers due to rapidly increasing demand and/or delivery problems.
Threat of customers switching to a competitor
If your competitors have a buffer, there is the threat that your customers will go elsewhere. You want to prevent that by investing time in accurate forecasting and purchasing planning (including safety stock).
Difficult to respond to a sudden demand increase
Without a buffer, it’s difficult to keep up with the market when there is a sudden surge in demand. It can result in lost sales and a stock shortage that affects the service levels of your company. If you are not able to meet customer demand, customer satisfaction drops which may result in a loss of turnover.
Safety stock is often determined based on the average number of sales, however, you can miss out on sales when the actual market demand is higher. Optiply’s AI purchasing algorithm allows you to make the right purchasing decisions by updating your purchasing advice real-time when market demand rises. The algorithm ensures that your stock level—and your safety stock—is in order.
6 tips to determine the safety stock
Earlier in this post, we explained the importance of safety stock. Keep on reading for six tips to determine the safety stock for your business.
Tip 1: Collect data
Collect both internal and external sales data. Know the market demand and sales figures of the products for which you want to determine safety stock. Find out the ‘regular’ demand and calculate any possible deviation.
Tip 2: Create a forecast
With a forecast, you get a clear picture of what you can expect to sell per month, week or day in a certain period. It is one of the main tools to plan your purchasing. Your safety stock should always be part of that purchasing planning.
Tip 3: Calculate the delivery time of your suppliers
The delivery times of your suppliers are essential for your planning. You want to inform and service your customers as best as possible, which means taking the delivery reliability of your suppliers into account. After all, you want your orders to be delivered on time.
Tip 4: Determine your service level
You want to meet customer demand and avoid lost sales. Are there situations when you accept that you can’t deliver products, or do you want to serve your customers at all costs? Determine the service level/market reputation you want for your business. That is an important indicator for determining the size of your safety stock.
Tip 5: Calculate the safety stock
There is a safety stock formula per product: k * σ * √ (R + L). The disadvantage of this formula is that it is a standard rule and not always complex enough.
Tip 6: Update your safety stock
When demand is uncertain, delivery reliability is even more important. This is how you keep your stock—and the buffer—at the right level. Optiply allows you to ensure more delivery reliability and to adjust your safety stock accordingly.
The safety stock helps you to respond to uncertainties within the supply chain and prevents the risk of stock shortages so you can continuously meet customer demand.
When updating the safety stock, focus on stability of both supply and demand at product level and to what extent trends and seasonality can influence them. Forecasting gives you a clear picture of your purchasing planning and what the size of your buffer should be.
In case of uncertain delivery times, it is extra important to focus on delivery reliability.
The purchasing software of Optiply can help you with this. The AI purchasing algorithm updates your purchasing agenda real-time. This keeps your safety stock up to date and prevents lost sales so you can continue to meet customer demand, keep your service levels and customer satisfaction high, and avoid turnover loss.
Veelgestelde vragen beantwoord
Heb je nog vragen over Optiply? We hebben de meest gestelde vragen voor je op een rij gezet.