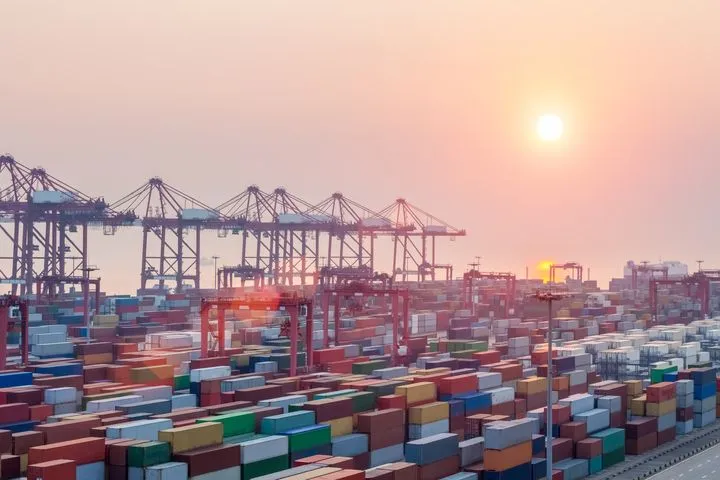
Delivery Reliability: What Is It and how do you measure it?
Business is booming, and orders are pouring in. The sales department is doing its job, and marketing campaigns are paying off. You have full confidence in your suppliers: you have a good relationship with them, and when you inquire about an order, they always respond politely. But when your phone keeps ringing with customers asking where their order is, you start to wonder.
Why are your delivery times consistently too long? In this article, you’ll learn what delivery reliability is and why you should track this important metric.
What is delivery reliability?
The delivery reliability of your suppliers refers to the extent to which the correct quantity of products is delivered at the right time. This takes into account customer needs and what you communicate to them. To ensure or improve customer satisfaction, you can assess your suppliers’ delivery reliability using various methods or checks.
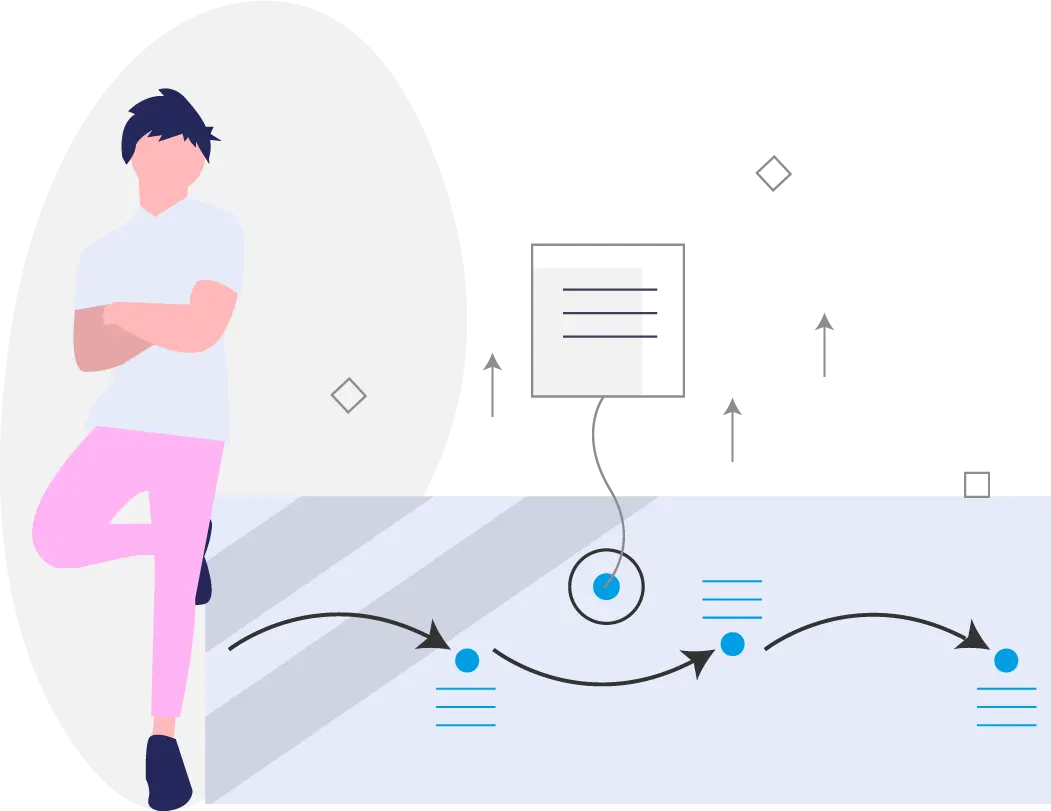
Why is delivery reliability important?
To serve your customers as effectively as possible, you want to avoid lost sales. Supplier lead times directly affect this. If a product is out of stock due to supply chain uncertainties, you risk losing sales, which is unfortunate.
The more reliable your suppliers are, the more your customers can rely on you.
Supplier reliability also greatly impacts the buffer stock you need to maintain. Less reliable suppliers require higher buffer stock, whereas reliable suppliers allow you to keep lower inventory levels. This principle can even be applied at the product level.
What happens if you don’t analyze delivery reliability?
For example, your website states that a product will be delivered within a week, but in reality, the delivery time often stretches to two or three weeks.
The issue isn’t the courier service but rather that your suppliers are delivering stock too late. You may be dealing with low delivery reliability.
In practice, many webshop owners know their suppliers well but don’t have a clear overview of which suppliers are causing delays. This knowledge is crucial for improving customer satisfaction. Poor delivery reliability can have serious consequences:
- Negative customer reviews
- Structural stock shortages, causing you to fall behind
- Poor balance between stock levels and purchasing costs
- Unclear delivery times
- Inability to prepare for seasonal demand spikes
- Stagnating growth or even a downward trend
How do you measure delivery reliability?
By continuously monitoring your suppliers and optimizing supplier management, you can achieve significant improvements. Before making optimizations, it's important to first assess your suppliers. What is the quality of your current suppliers, and how do you measure their performance?
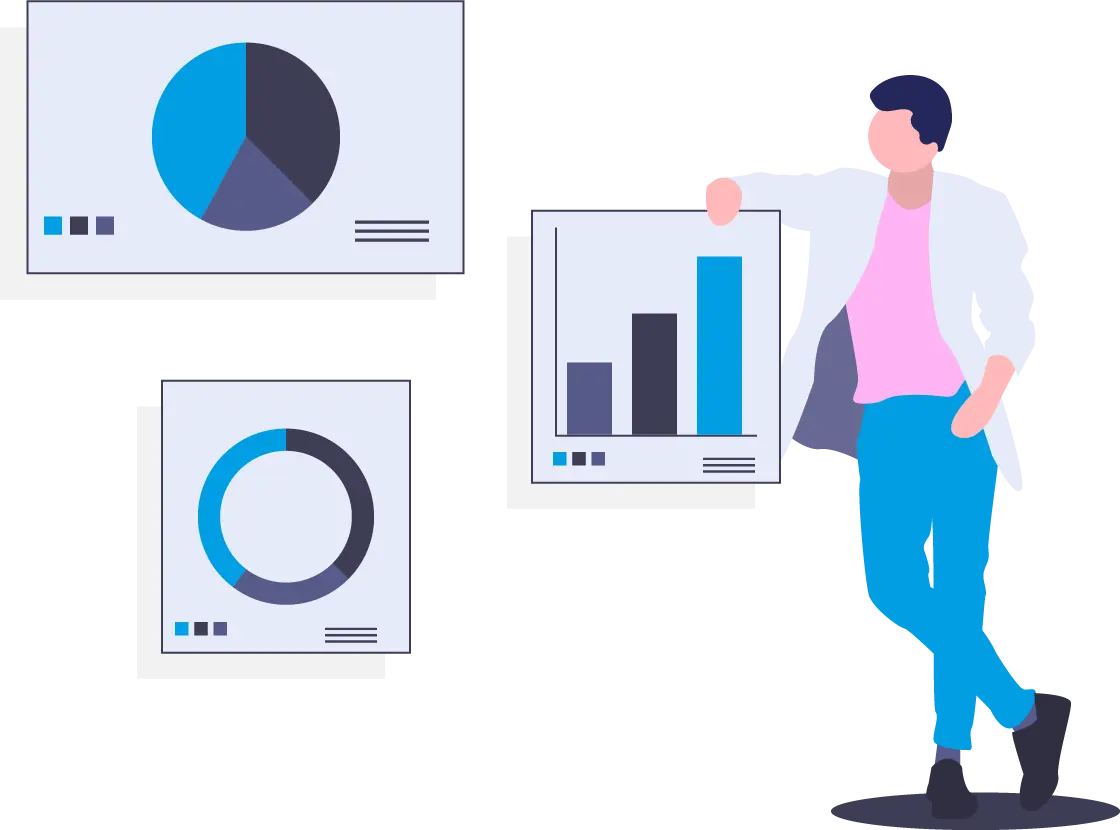
Categorize your suppliers using the ABC analysis
An ABC analysis categorizes suppliers based on importance. The A-suppliers are a small group that accounts for the majority of your purchasing budget, while the B- and C-suppliers are less critical.
First, enter the purchase volume per supplier and sort them by size. The first 70% of the total volume are your A-suppliers, the next 20% are B-suppliers, and the remaining 10% are C-suppliers.
Your A-suppliers deserve your full attention, while you might consider replacing underperforming suppliers in the C-group.
Compare suppliers
Next, evaluate supplier performance by category. Create a comparison table that includes delivery time, price, costs, order quantities, minimum order requirements, service level, payment terms, and financial health.
Don’t just compare your existing suppliers - also look at new competitors to identify opportunities for replacement.
Once you have a basic analysis, dive deeper into specific suppliers by assessing uninterrupted supply chains, collaboration, and quality management.
Centralize data
You may have collected supplier data in an Excel sheet or shared spreadsheet. While useful initially, serious supplier management requires centralization and automation. Use automated software to track supplier data, including lead times, delivery schedules, and stock levels.
Manual tracking is time-consuming, but an algorithm can make the process more efficient.
Evaluate your suppliers
Are deliveries taking too long, or is it time to stock up more inventory? Keep track of these issues closely. Regularly evaluate suppliers to maintain a strong relationship and address areas for improvement. Useful tools for this include:
- Supplier scorecards: periodic evaluations of key factors,
- Contract management: working with contracts that include regular evaluations,
- Six Sigma: assess the entire business process.
Additionally, request your suppliers' feedback to understand their collaboration perspective. Their input can be valuable in optimizing your business processes.
By following these steps, you gain better oversight of your suppliers and make strategic decisions that result in higher efficiency and lower costs.
Eleven ways to improve delivery reliability
Prevention is better than cure. If you're just starting your webshop, ensure a strong foundation by managing suppliers effectively:
1. Involve senior management in the process to align with company goals.
2. Communicate your expectations to suppliers.
3. Get to know your suppliers and maintain regular contact.
4. Share best practices from one supplier with others to encourage improvement.
5. Implement a tracking system to measure delivery reliability directly.
6. If a supplier’s reliability is consistently low, address the issue and take action.
7. Continuously analyze the entire supply chain using automated software.
8. Dedicate specific hours each week to measuring and managing supplier performance.
9. Compare multiple distribution channels for international suppliers, weighing the costs of sea, air, and rail transport.
10. Evaluate different suppliers of the same products based on price, delivery time, and other key conditions.
11. Document everything in a Service Level Agreement (SLA).
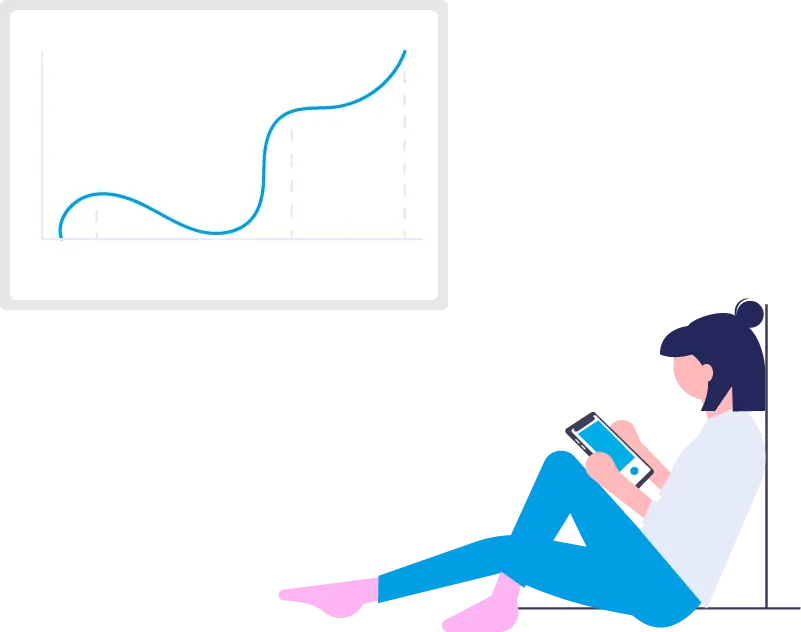
Maintain control over delivery reliability in your supply chain
For webshops and wholesalers, preventing stockouts is always a challenge. Managing supplier relationships effectively can make all the difference.
Failing to do so can impact your supply chain and the buffer stock you need to maintain. By analyzing your delivery reliability, you can avoid unexpected issues.
Gaining control over delivery reliability helps you oversee the purchasing process, balance procurement and inventory costs, minimize risks, and keep customers satisfied.
Veelgestelde vragen beantwoord
Heb je nog vragen over Optiply? We hebben de meest gestelde vragen voor je op een rij gezet.